How Local Packaging Equipment Repair Services Offer Faster Turnaround Times
How Local Packaging Equipment Repair Services Offer Faster Turnaround Times
Blog Article
Discover Why You Need Reliable Packaging Devices Fixing Services for Optimum Production
In the competitive landscape of manufacturing, dependable packaging devices repair services play an essential function. Timely treatments can significantly decrease devices downtime and improve production efficiency. Many companies ignore the significance of attending to mechanical failings quickly. This oversight can bring about significant operational challenges. Comprehending the nuances of repair work services and their ramifications on production could be critical for companies aiming for sustained success. What aspects should services think about to assure they select the ideal repair work solution?
The Relevance of Timely Repair Works in Production
Although equipment malfunctions are usually inevitable, the importance of timely fixings in manufacturing can not be overemphasized. When tools breakdowns, the entire assembly line can be interfered with, causing pricey delays and decreased productivity. Suppliers rely upon their equipment to run efficiently; consequently, prompt repair services are necessary to lessen downtime.Delays in addressing tools problems can escalate right into bigger troubles, impacting product top quality and operational performance. Timely repairs not just recover capability yet likewise extend the lifespan of the equipment, ultimately decreasing long-term expenses related to substitutes. Additionally, maintaining equipment in suitable condition supports office safety, as malfunctioning devices can position hazards to employees.In the competitive landscape of production, prioritizing prompt repair services is vital for sustaining procedures and conference customer demands. Investing in reliable repair service services is a strategic move for producers intending to boost effectiveness and keep high production criteria.
Usual Problems With Product Packaging Devices
Packaging devices often experiences a range of common issues that can prevent manufacturing performance. One prevalent issue is mechanical failure, which might occur from used components or insufficient upkeep. This can result in malfunctions that interfere with the product packaging process. An additional usual problem is misalignment, where product packaging machinery stops working to operate correctly as a result of improper arrangement, causing item damage or waste. On top of that, sensors and controls can malfunction, resulting in unreliable measurements and operational errors.Over time, damage can likewise trigger conveyor belts to slide or jam, influencing the circulation of products. Furthermore, software glitches in automated systems might cause hold-ups or wrong product packaging setups. Routine tracking and timely repair work can reduce these issues, making sure smoother operations. Dealing with these typical concerns proactively is necessary for preserving excellent performance in product packaging operations.
Exactly How Tools Downtime Influences Your Organization
How does devices downtime influence an organization's total productivity and profitability? Equipment downtime can considerably impede a firm's procedures, leading to lowered production outcome and postponed shipment times. When equipment fails, staff members might be forced to stand idle, throwing away important labor hours and affecting workforce spirits. This disruption can waterfall via the supply chain, leading to unmet customer demands and prospective loss of contracts.Moreover, the economic ramifications of devices downtime prolong beyond immediate losses. Companies might experience increased functional costs due to overtime repayments or expedited delivery to fulfill orders. In highly open markets, extended downtime can stain an organization's credibility, driving clients towards more dependable rivals. Ultimately, the mix of lost productivity, boosted costs, and possible reputational damages underscores the vital need for prompt and effective product packaging equipment repair work services to preserve peak operations and assure continual profitability.
Cost-Benefit Evaluation of Professional Repair Providers
Reviewing the financial effects of equipment downtime discloses the significance of professional repair service solutions. Delays in manufacturing can bring about substantial income losses, affecting the overall profitability of a business. Spending in specialist fixing services not just reduces downtime yet also guarantees that devices operates at peak efficiency.While the initial price of working with knowledgeable technicians might seem high, the lasting advantages commonly exceed these expenses. Dependable repair work prolong the lifespan of equipment, decreasing the demand for costly replacements. In addition, professional servicing can avoid unanticipated breakdowns that interfere with operations and sustain additional costs (Packaging Equipment Repair Services).Companies that focus on professional fixing solutions commonly experience improved item high quality and uniformity, boosting consumer satisfaction. Ultimately, a well-executed cost-benefit analysis highlights that the financial investment in professional repair service services is not just a cost, yet a strategic technique to guarding manufacturing performance and economic stability in the competitive product packaging market
Selecting the Right Repair Work Provider
When choosing a fixing provider, what essential factors should services think about to assure ideal outcomes? The provider's experience and experience in servicing specific packaging equipment is essential. A company with a tried and tested performance history in the industry can assure that fixings are conducted effectively and successfully. Additionally, evaluating the provider's qualifications and training can show their commitment to preserving high standards.Second, responsiveness and accessibility play a vital role. A reliable repair service must use quick feedback times and versatile scheduling to decrease downtime. Third, businesses must evaluate client reviews and endorsements, as these can give understandings into the service provider's reliability and high quality of service.Finally, transparent prices and guarantee choices are essential. A trustworthy supplier ought to stand and use clear price quotes behind their work, assuring that companies receive value for their financial investment. By taking into consideration these aspects, business can select a repair solution that meets their details requirements.
Preventative Upkeep to Extend Equipment Life-span
Preventative maintenance plays an essential role in extending the life expectancy of product packaging equipment. Implementing routine examination timetables, lubrication, calibration, and strategic part Find Out More replacement can greatly reduce downtime and repair work expenses. By prioritizing these practices, businesses can enhance functional efficiency and warranty trustworthy efficiency.
Routine Evaluation Schedules
Normal inspection routines play an essential duty in the longevity of packaging devices, ensuring suitable performance and minimizing the chance of unexpected breakdowns. By sticking to a systematic assessment routine, services can determine damage, deal with prospective concerns, and maximize devices capability. These assessments generally involve checking important elements, assessing efficiency metrics, and examining overall equipment problem. Routine evaluations help develop a baseline for efficiency, making it much easier to discover variances that might signify a problem. Packaging Equipment Repair Services. Furthermore, scheduled assessments can facilitate much better planning for repair and maintenance, minimizing downtime and enhancing performance. Ultimately, executing normal inspection schedules adds to a positive maintenance method that promotes operational effectiveness and extends the life-span of packaging equipment
Lubrication and Calibration
Effective maintenance routines, such as routine examinations, normally bring about the demand for lubrication and calibration to guarantee peak efficiency of packaging tools. Lubrication decreases friction, decreasing wear and tear on relocating parts, which can substantially expand the life-span of equipment. find more Regularly used lubricating substance assists maintain operational effectiveness, stopping overheating and potential breakdowns. Calibration, on the other hand, guarantees that equipment operates within specified parameters, thereby boosting precision and uniformity in manufacturing. Failing to effectively oil or adjust can result in expensive downtimes and repair work. Integrating these practices right into a preventative upkeep approach promotes dependability, raises efficiency, and ultimately supports a stable production atmosphere. Prioritizing lubrication and calibration is necessary for preserving optimal equipment performance.
Element Substitute Methods
A positive method to element replacement plays a necessary duty in extending the life expectancy of packaging equipment. Consistently evaluating the condition of essential parts, such as seals, belts, and electric motors, makes it possible for drivers to determine wear and prospective failures before they compromise production. Carrying out an organized schedule for part replacement, based upon manufacturer recommendations and usage patterns, can substantially decrease downtime and repair prices. Furthermore, using premium substitute parts assurances compatibility and performance, additionally improving operational performance. Training personnel to identify early signs of wear and assisting in timely substitutes not only stops unforeseen malfunctions however additionally advertises a society of upkeep understanding. Inevitably, efficient part substitute strategies contribute to continual productivity and integrity in packaging procedures.
Case Researches: Success Stories From Effective Services
Checking out real-world examples reveals the considerable influence of effective product packaging devices repair work on operational performance. One significant instance involved a beverage company that faced frequent device breakdowns, leading to considerable production hold-ups. By partnering with a reputable fixing solution, they implemented a precautionary upkeep strategy that lowered tools downtime Get More Information by 40%. In another instance, a treat manufacturer experienced traffic jams as a result of malfunctioning securing devices. After spending in specialized fixing services, they enhanced machine efficiency, resulting in a 30% boost in output.These instances illustrate that effective and prompt fixings not just bring back performance but likewise add to enhanced production rates. By focusing on efficient repair services, companies can reduce operational disruptions and cultivate an extra effective setting. Such success stories highlight the relevance of purchasing reputable packaging equipment fixing solutions to protect long-lasting operational performance.
Regularly Asked Concerns
What Credentials Should I Try To Find in Repair Service Technicians?
When considering repair service technicians, one should prioritize certifications in pertinent machinery, experience with specific tools, analytic abilities, and a strong performance history of dependability (Packaging Equipment Repair Services). Great communication and adherence to safety and security requirements are likewise vital certifications to seek
Just How Can I Recognize When My Equipment Requirements Services?
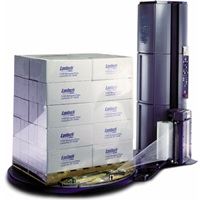
What Types of Packaging Equipment Require Specialized Repair Work Solutions?
Exist Guarantees for Fixing Services on Product Packaging Equipment?
Warranties for repair services on packaging devices differ by supplier. Commonly, trusted business supply service warranties to ensure top quality and dependability, covering parts and labor for a specified period, thereby improving client self-confidence in their services.
Just how Do I Arrange Emergency Situation Repair Services?
To arrange emergency repair services, one normally contacts the service company straight by means of phone or their web site. Prompt interaction warranties a quick reaction, enabling timely resolution of equipment issues and minimizing production disruptions. In the affordable landscape of production, trusted product packaging devices repair service services play a necessary function. In addition, maintaining tools in excellent problem supports office security, as malfunctioning devices can pose dangers to employees.In the affordable landscape of manufacturing, prioritizing prompt repair work is essential for maintaining operations and meeting client needs. After investing in specialized repair solutions, they enhanced device efficiency, resulting in a 30% increase in output.These instances illustrate that efficient and prompt repairs not just restore capability yet additionally contribute to enhanced manufacturing rates. Certain kinds of packaging equipment, such as vacuum sealers, labeling makers, and automated conveyors, usually call for specialized repair solutions. Service warranties for fixing services on packaging tools differ by copyright.
Report this page